Jobs in Abu al Matamir
Refine Search By
Industry
Job Title
Experience
Nationality
Job Type
Posting Date
Gender
Jobs in Abu al Matamir
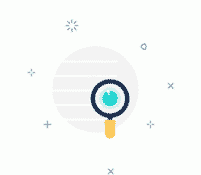
Less results matching your search!
Try removing some of the filters to get more results
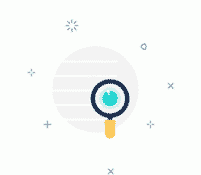
No results matching your search!
Try removing some of the filters to get more results
Inside Sales Representative Fluent in English Bachelor’s Degree in science, marketing, business or related fields. 2-3 years of previous experience in Account management and new business acquisition Strong listening and sales skills including financial negotiation skills, More...
Commercial Finance Senior Analyst B.Sc. or equivalent degree in Economics, Finance, or Accounting, The right candidate will have at least 8 years of experience in FP&A and Commercial Finance roles with a great skillset to manage senior stakeholder and perform complex analysis More...
Job Responsibilities:Implement HR policies and procedures to ensure compliance and proper guidance for employees.Handle employee complaints effectively and in accordance with company policies and local laws.Provide advice and support to employees and management regarding workplace iss More...
We are hiring a Utility Helper/Driver for an area As our Utility Helper/Driver you will be responsible for delivering food/meals and supplies to several locations, clinics, and In addition, this position supports all other functions of the department as needed or directed by *Ensure More...
Job Scope/Purpose: Handle customers efficiently based on a high quality service standards through showing high knowledge of product and high skills of sales or customer service in accordance to the processes and targets of the contact center and Centro clients expectationsJob Qualific More...
Responsibilities: Compounding and dispensing medications, as prescribed by physicians. Monitoring customers’ drug therapies, advising interventions, and informing customers of any potential side effects. Instructing customers on how and when to take prescribed medications. More...
Kids’ Work is a mother-daughter-owned center, serving families for over 30 years; we pride ourselves on creating a childcare experience that is authentic, genuine, and Our administrators have their roots as Kids’ Work classroom teachers and know how to provide an organize More...
Technical Project Specialist 3 years of end-to-end project management experience in a Tech Company Solid understanding of the entire Software Development Lifecycle (ideally as a software engineer) Proficiency in delivering systems integration projects & managing integration More...
Engineering Manager - Cairo Great product sense for selecting the opportunities which deliver impact to our engineers Empathetic and able to easily build relationships (Stakeholder & Dependency Management) Able to balance between continuous product discovery and delivery E More...
Announcing the Launch of Our New Platform! We are excited to announce the launch of our highly anticipated volunteer programs on the Egyincs Platform, a specialized platform for disseminating various opportunities including training, jobs, volunteer opportunities, scholarships, artic More...
Frontend Developer Job Responsibilities: 1 Build cuttingedge applications.2 Developing new userfacing features.3 Building reusable components and frontend libraries for future use4 Translating designs and wireframes into highquality code5 Optimizing components for maximum performance More...
If youre a professional editor we have an exciting opportunity to use your language skills in a new and innovative way. Instead of thinking that AI will replace you here you can help shape the future of AI.We re seeking freelance editors to collaborate with us creating a diverse ran More...
If youre a professional editor we have an exciting opportunity to use your language skills in a new and innovative way. Instead of thinking that AI will replace you here you can help shape the future of AI.We re seeking freelance editors to collaborate with us creating a diverse ran More...
If youre a professional editor we have an exciting opportunity to use your language skills in a new and innovative way. Instead of thinking that AI will replace you here you can help shape the future of AI.We re seeking freelance editors to collaborate with us creating a diverse ran More...
If youre a professional editor we have an exciting opportunity to use your language skills in a new and innovative way. Instead of thinking that AI will replace you here you can help shape the future of AI.We re seeking freelance editors to collaborate with us creating a diverse ran More...
We are seeking a highly motivated and experienced Senior Social Media Specialist to join our growing marketing team. The ideal candidate will be responsible for developing and executing comprehensive social media strategies across various platforms to achieve our marketing goals More...
About Our Client: This is a fulltime onsite role for a FMCG Graphic Designer at World Link Distribution located in El Sadat City. The Graphic Designer will be responsible for creating visual concepts using graphic design software and tools to create graphics logos and brandin More...
Company Description We suggest you enter details here Role Description This is a fulltime onsite role located in Heliopolis for an Investment Analyst at confidential The Investment Analyst will be responsible for conducting research on companies and industries to evalua More...
Job Scope/Purpose: Handle customers efficiently based on a high quality service standards through showing high knowledge of product and high skills of sales or customer service in accordance to the processes and targets of the contact center and Centro clients expectationsJob Qualific More...
Job Summary:We are seeking an experienced and versatile HR Specialist to join our team. The HR Specialist will be responsible for managing various HR functions and providing support to employees and management across the organization. The ideal candidate will have a solid understandin More...
Dr.Job Pro is an online platform that connects employers with skilled job seekers, facilitating the search for job opportunities and top talent. Established in 2015. Dr.Job Pro has emerged as the Gulf region's premier job portal, attracting thousands of job seekers every day from different countries in Middle East and world wide.
Follow Dr.Job
Dr Job FZ LLC. 2024 © All Rights Reserved
Jobs by Countries
We Value Your Privacy
We use cookies to enhance your browsing experience, serve personalied ads or content, and analyze our traffic. By clicking "Accept All", you consent to our use of cookiesCookie Policy
Customize Consent Preferences
We use cookies to help you navigate efficiently and perform certain functions. You will find detailed information about all cookies under each consent category below.
The cookies that are categorized as "Necessary" are stored on your browser as they are essential for enabling the basic functionalities of the site.
We also use third-party cookies that help us analyze how you use this website, store your preferences, and provide the content and advertisements that are relevant to you. These cookies will only be stored in your browser with your prior consent.
You can choose to enable or disable some or all of these cookies but disabling some of them may affect your browsing experience.
For more information on how Google's third-party cookies operate and handle your data, see: Google Privacy Policy
Necessary
Necessary cookies are required to enable the basic features of this site, such as providing secure log-in or adjusting your consent preferences. These cookies do not store any personally identifiable data.
Analytics
Analytical cookies are used to understand how visitors interact with the website. These cookies help provide information on metrics such as the number of visitors, bounce rate, traffic source, etc.
Advertisement
Advertisement cookies are used to provide visitors with customized advertisements based on the pages you visited previously and to analyze the effectiveness of the ad campaigns.